- By Dan Veaner
- News

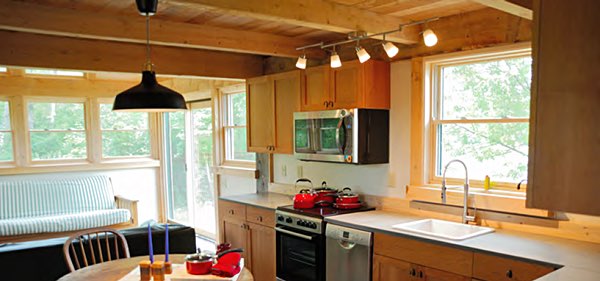
The Town of Lansing is negotiating with developers to finally sell parts of the 153 acre parcel of land across State Route 34B from the Town Hall campus and ball fields. Two are further along in negotiations than others, and last week developers of one of them presented a preliminary view of their project to Town officials. The Lansing Cottage Community project will likely begin with 10 single family homes, then, if the market will bear future phases, expand to a 60 home community.
The builder is called Tiny Timber, LLC, but these are not tiny houses. 'Tiny houses' tend to be only around 200 square feet, and built to travel on wheels. Designs start at about 600 square feet for a cottage style home. The Lansing project will be more in the 1,000 to 1200 square foot range, and possibly up to 1900 square feet if a home includes a finished basement. The developer's aim is to provide smaller, good quality affordable homes targeted at young people looking for a first home or older homeowners who want to downsize.
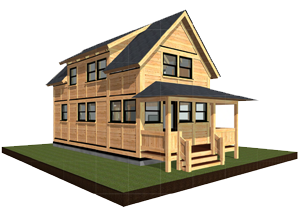
The group is working on two community projects, including the Lansing project and another in Varna. The Lansing project is expected to be a series of shotgun-style homes on small lots on a total of 10 acres of land. The developers anticipate building 10 homes in the first phase. Assuming the market is receptive they would build 20 more in phase two, and 30 more in a third phase. The homes would be built in groupings, each group having homes facing a common green space, with parking lots that include a T-turnaround meeting the specification needed for fire trucks to turn around. No home would be more than 150 feet away so emergency responders could reach with standard fire hoses.
Amenities may include a playground and a centrally located half-basketball court. Sidewalks are planned, making the community walkable. The preliminary idea is for access to come from Conlon Road, but traffic and a horrendous turn from Conlon onto 34B was discussed at some length, with town officials recommending that access from the east (or both) would make more sense. One solution may be a connecting road to the Cornerstone project road that will likely join a new public road that lets out on Auburn Road that would create a four-way intersection with Woodsedge Drive.
"People on Conlon Road are very concerned about the amount of people that are going to come there," said Lansing Supervisor Ed LaVigne. "Of course we share that concern. Does traffic come out from Conlon Road onto Auburn Road, or is there another access that they can get to sooner than later. So a connecting road may be something you want to think about, maybe in phase two. Ten houses is not an impact -- that's a cul-de-sac. But when you're talking 30 houses, now you have the impact. That question will come up at your public hearing for the Planning Board."
At this stage, details such as road access and even the final design of the homes are still in the preliminary planning phase.
In contrast to the Cornerstone project that could bring 128 rental units in multi-unit buildings to the east, the homes in the Lansing Cottage Community project will be sold to individual owners. The developers said they are considering a range of $175,000 to $225,000, with the most expensive homes including a finished basement. Green spaces homes are grouped around will double as septic leach fields. A homeowner association will manage manage the storm water, septic, parking, and the road, if it ends up being a private road.
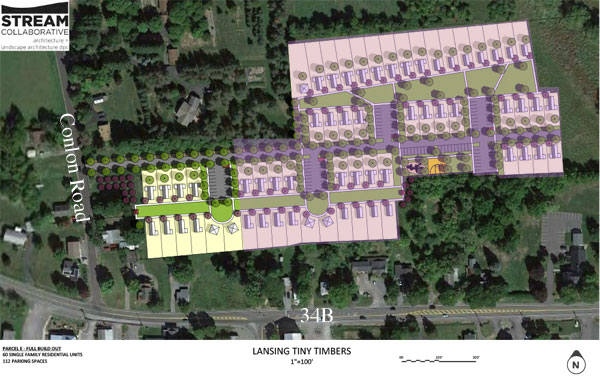
Dolph has sold seven homes built around the kit he has been developing, with an eighth about to be sold. One of these homes is currently under construction in the Farm Pond Circle development in Lansing. These prototypes have been used to develop a kit system that uses modular components assembled in a shop, then erected on-site.
Noah Demarest, a local architect and owner of STREAM Collaborative presented the project. Demarest has worked with Dolph on home designs as he developed the designs for a unique post and beam system. They were joined by project manager Michael Culotta, urban planner David West, and Warren Real Estate General Manager and VP of Sales Brent Katzmann.
"What's unique about this system is that it's a high performance wall system that has a continuous insulation that wraps the entire building," Demarest explained. "There is no thermal bridging between the inside and outside of the building. The way that's achieved is with a structural skeleton on the outside and a structural skeleton on the inside. Form insulation can wrap all the way around the building."
The posts and the beams are exposed. Every member is slotted so hemlock siding slides down in these slots. There are no nails holding that siding, allowing green hemlock lumber to settle as it dries. A spacer board is placed at the top of each course of siding so a gap is created at the top. The builders return to add a piece of siding at the top if the wood settles enough that there is room for it. Copper protects the horizontal surfaces of the wood.
"It's almost all locally sourced green hemlock," said Demarest. "Since it's green it adds significantly to the affordability. It doesn't have to be kiln dried. It's rough cut. It comes straight from the saw mill to the factory."
The kit construction also makes the homes more affordable. Kit components repeat throughout the design, using a simple approach based on the width of standard 3 foot wide windows. A 3 foot pattern repeats all the way around the outside.
"That is where the affordability comes in, the production aspect where a lot of these component parts can be mass produced, and then assembled in different configurations," Demarest said.
Using a special crane the homes can be completed in about eight weeks. When Dolph's excavation/basement crew finishes it moves to the next home while an assembly crew uses a special crane to erect the pre-built walls and roof. The crews then rotate again, with a finish crew working on the first house while the other two crews move to the second and third. The developers say that by using this rotation system, a new home can be completed every three weeks.
"It is a kit that's fabricated in a shop," Demarest said. "But then it's assembled on-site. It's not too different from a traditional method of building once you're on-site, but most of the hard work is done very quickly. Buzz has this machine that can lift an entire wall assembly. So the walls are built on the ground, and then tipped up into place. Then the roof is dropped into place."
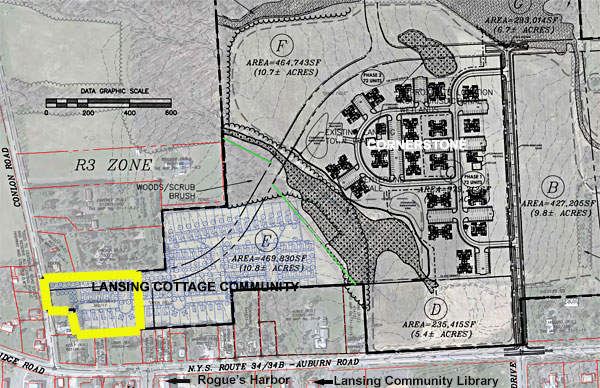
Culotta says the purchase agreement, which will be signed when a new LLC is formed for the Lansing project, is good for 24 months. He said the hope it to exercise that contract in that time period. Once that is done work on the first phase can begin. Amenities like the playground, gazebos and a half-basketball court would come in future phases.
"Our goal would be that everything would be built out within five years," Demarest said. "We're talking about two or three phases. It's not going to be 10 homes at a time. The first ten homes makes sense, but then the next phase might be 20 homes. The last phase might be the rest of them, 30 homes. I would imagine this amenity would happen in phase two."
LaVingne said that despite some issues needing to be worked out, he thinks the project is a good fit for Lansing. The next step will be for the new LLC, once it is formed, to sign the purchase agreement with Lansing. During the next year or two specific issues will be worked out and designs finalized as the company works with the Town Planning Board.
v13i29