- By Dan Veaner
- Around Town

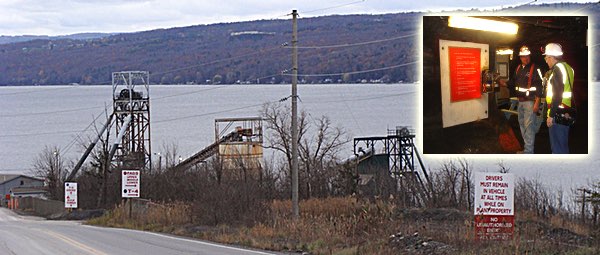
Once you get to work it takes almost another hour to get to work. Because after about five minutes taking the elevator to the nearly 100 year old Cayuga Salt Mine -- the deepest rock salt mine in the United States -- you have another 45 minute ride through seven and a half miles of tunnels before you arrive at the active mining site. Round trip, that's nearly two hours of daily commuting, plus however much time it takes you to get to the mine from home. Controlling the air flow over that distance is difficult, and the drop in voltage in seven and a half miles of electrical cables is significant, posing safety challenges for workers. If something unfortunate should happen, miners have to evacuate using the same route, and with all three mine lifts at the southern end of the mine, escape routes are limited.
That's why Cargill Deicing wants to build a new $42 million mine shaft close to the current active mining area that will provide a safer work environment, cut the commuting time, and an ample supply of electricity and air for another century. In 2012 Cargill officials met with neighbors to get questions answered about the 2,500 foot deep elevator shaft that would soon be their new neighbor. Last week over 30 neighbors and town officials came back for an update.
"Were waiting for the process to play itself out to give a status update when we knew what the permit status was," says Mine Manager Shawn Wilczynski. "But we felt, since it was taking so long, it was prudent to invite our neighbors back. We met primarily with neighbors we had (originally) reached out to and some other stakeholders including Town of Lansing representatives and some other folks. I'm very appreciative that we did. Cargill strives to be a responsible company and a good neighbor."
Three key concerns are additional traffic, noise, and a potentially ruined view. Wilczynski was joined for three sessions last week by Senior Mine Engineer Dave Plumeau, as well as the shaft project manager, an environmental consultant, legal consultant, engineer.
"We tried to have all the right people here to answer any of the questions or concerns that the community might have had," Plumeau says.
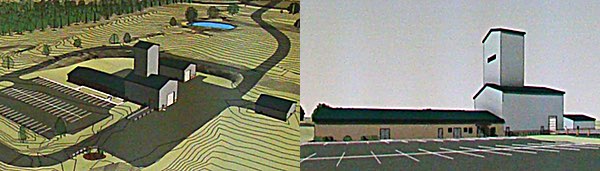
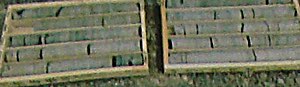
"Some of the neighbors felt this was opening the door to create this as a production facility," Wilczynski says. "The surface land here is just not large enough or supportive. It doesn't have access to the railroad. And it would require completely different permitting and review process, so, again, there is no intention of doing that at this time."
With a 20,000 pound total lift capacity, the new elevator will be able to carry large equipment as well as miners. But Wilczynski says the company only buys such equipment every five years, and from a neighborhood impact standpoint, lowering it into the mine would just be another elevator ride.
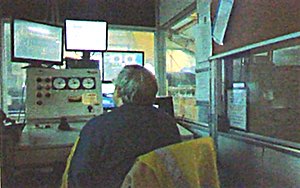
"We have almost 220 years of total shaft experience here if you look at the three shafts we have on our facility. There are always lessons learned," says Wilczynski. "We had great intentions. We had all the right processes in place. What's changed are the tools we are using to be more quantitative and qualitative, rather than more of a judgement call. We've established improved inspection approaches with improved tools and improved acceptance criteria, and that will certainly be leveraged and carried over to the new system, including our selection of what type of guide system we would use."
Surprisingly that will mean that the new lift will use Australian kerry wood guide rails instead of the steel rails used in the existing shaft. Wilczynski says the wood rails are more predictable than steel, and if there is a problem, the steel brakes dig into the wood, rather that relying entirely on clamping the brakes to the rails to bring the cage to a stop slowly enough to prevent injury to passengers. If that should happen that section of the rail would be replaced afterward.
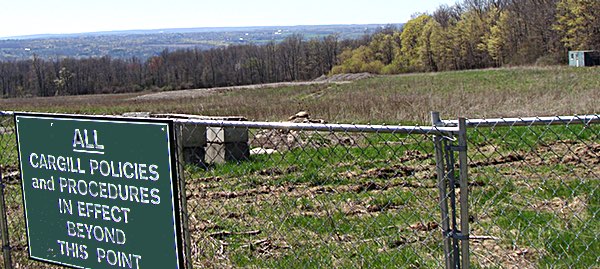
The company is addressing visual and noise concerns by enclosing the new shaft inside a building that could easily be taken for a farm building. Cargill owns a 57 acre plot on Ridge Road, south of the Cayuga Power Plant. 12.3 acres of that will be impacted by the shaft, well away from the road. Unlike the bare machinery at the main mine facility south of Myers Park, all the equipment will be enclosed in buildings designed to look like farm buildings. One will enclose the shaft and elevator mounted in it, along with the hoist operator's booth. The hoist is computer controlled with many safety features built in.
Another will house the electrically-powered winder hoist, and a third building will include offices, lockers, and showers where miners will change and don equipment they must wear when working in the mine. Enclosing the equipment inside these buildings will also reduce the noise factor. The locked buildings will also add another measure of security to the site.
Neighbors were shown architects' renderings last week, plus various views from their neighborhood and across the lake showing what the facility will look like from different viewpoints. Enclosing the equipment in these buildings is also calculated to dampen noise created by the lift inside.
"The design takes a lot of factors into consideration as far as outward aesthetics," Wilczynski says. "We've been to the Town of Lansing Comprehensive Plan meetings and we know people want this to retain its rural/agricultural feel. As far as we're concerned, we're doing everything we possibly can to make it look more like a farm property more than the mine facilities we currently have."
Most of the 8% increase in traffic will be automobile traffic, three shifts of employees commuting to and from the site. The company is looking at scheduling work shifts to cause the least impact to peak traffic times.
"We have the intention of being the best neighbors possible," Wilczynski says. "We'll adjust work schedules so construction only takes place from 7 in the morning to 7 in the afternoon."
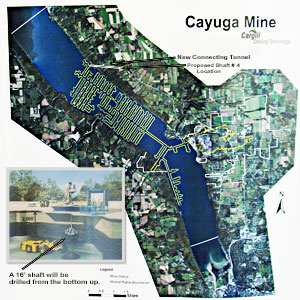
"The last thing we want is to have a negative impact," Wilczynski says. "And we certainly don't want to move forward spending $42 million if we think it would have an impact to the mine or an impact to the lake. The environmental assessment was to do the proper diligence to make sure this site is viable to support a shaft. The first thing we did was to drill a core hole and absolutely verify the geology and hydrology in the area, that there are no gas or water pockets."
Constructing the shaft will take about a year. In the first two months an approximately 11 inch pilot hole will be drilled. Over the next three months a circular shaft about 16 feet in diameter will be drilled using a raised bore process, also from the bottom up. Using this method is considered the lowest risk way to drill a shaft, and has the least environmental impact on the surface. Removed materials fall back into the mine, where they are disposed of.
"Reaming of the shaft can take place around the clock, because it's more quiet than people believe," Wilczynski explains. "That was another reason we wanted to up-ream the shaft. There isn't the drilling and the blasting that is associated with conventional shaft sinking."
The hole is then lined with concrete and brackets for the wooden shaft guides are installed. The concrete liner is about a foot thick, leaving a 14 foot in diameter shaft. This stage takes six to eight months, after which the construction equipment is removed and the final pieces of equipment are installed. Shaft operators and mechanics are trained, and ventilation changes to the mine below are completed.
Company officials say that the new shaft will mean retaining the 200 current employees, while adding at least four new jobs including new hoist operators and a person to accept materials during the day. A 2014 independent economic analysis found that the mine accounts for an impact of $4.5 million in the Town of Lansing, $173 million in Tompkins County, and $221 million in New York State.
If all goes well company officials expect Shaft #4 to be operational by early 2020.
v13i17